Sorry, that story no longer exists on our website
The article or video you are looking for has been moved to our archive. Perhaps another story on this page might interest you?
Scroll down for links to our latest news, crisis explainers and videos from our projects.
Latest news and stories from MSF Ireland
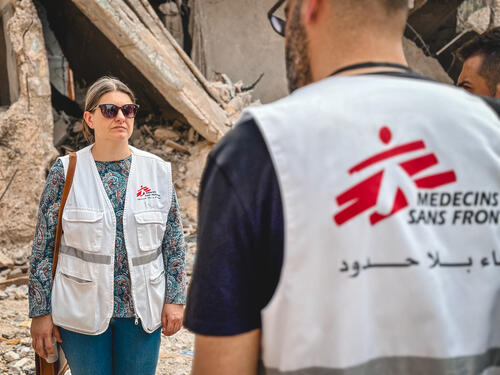
MSF reports that over five months of military operations in the northern West Bank, have displaced more than 40,000 Palestinians, destroying homes, clinics, water systems and trapping families without shelter, essential services or healthcare.
Learn more
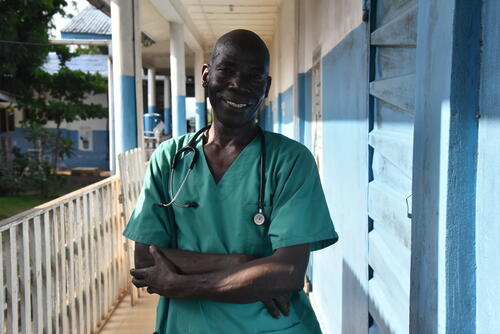
Learn about Claude Ndoko, a community health officer in the paediatric intensive care unit at Magburaka government hospital in the Northern Province of Sierra Leone. Claude’s journey with MSF started 22 years ago.
Learn more
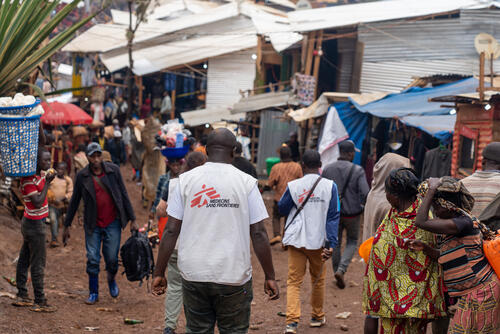
In Lomera, South Kivu (DRC), a gold rush brought thousands of people to the area—without proper sanitation. Now, a cholera outbreak has struck. MSF is responding with treatment, vaccinations, and clean water solutions
Learn more
Never miss another story
Sign up to Frontline, our monthly e-newsletter, to stay up to date with MSF's life-saving work in over 65 countries
MSF crisis responses explained
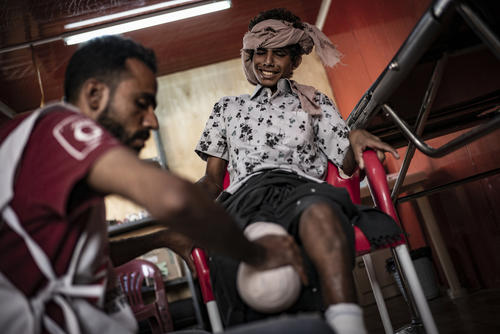
Years of conflict have left millions in Yemen without food, water, or healthcare. MSF is saving lives every day— learn more and support our work.
Learn more